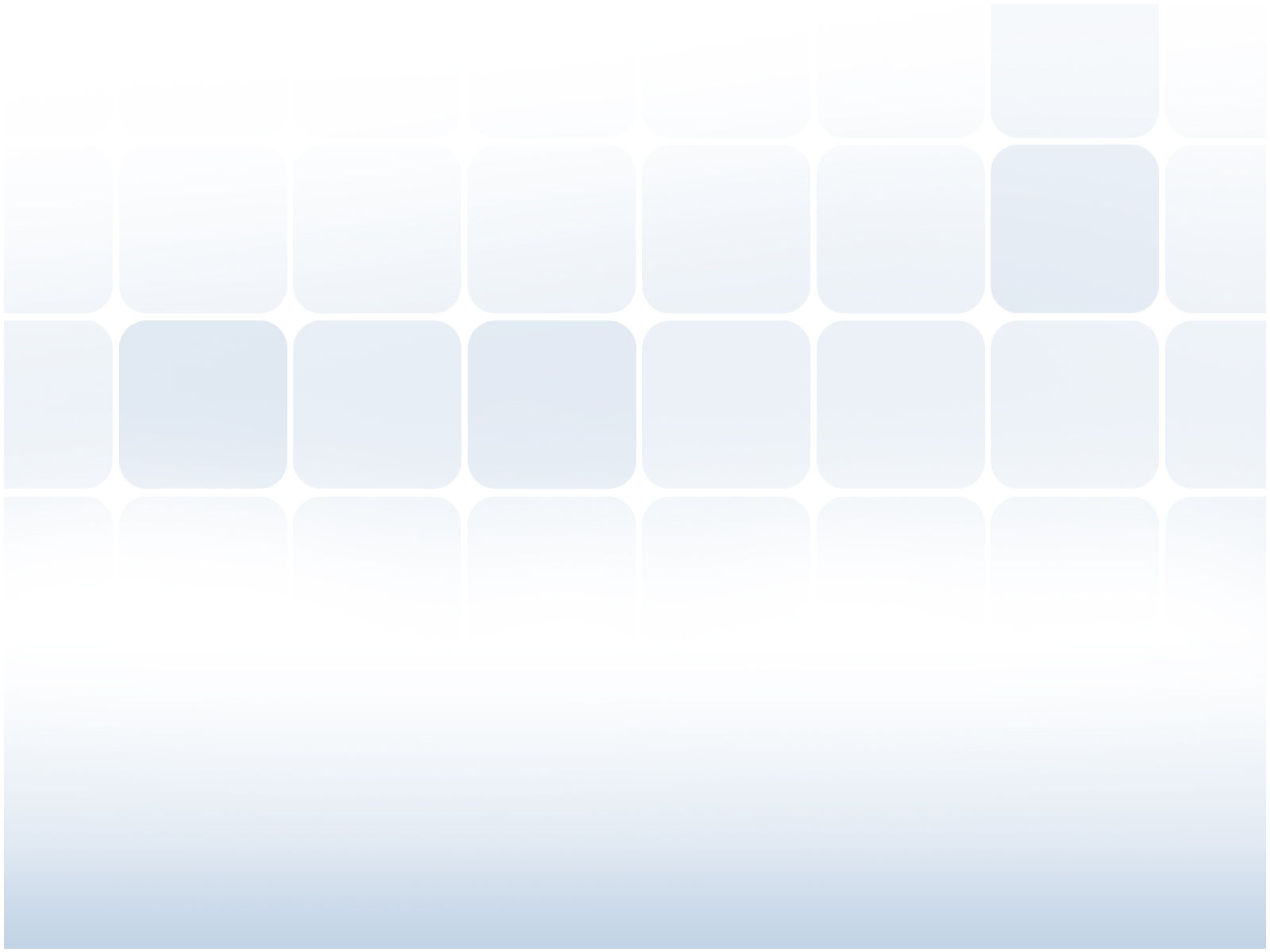
Workshop Safety and Machine Tools
In the first three years of their course, all students undertake training in the use of both woodworking and metalworking machine tools. Students are required to carry a copy of their Record of Workshop Experience with them during School Experience. It contains details of machine tools in which they have been trained. This booklet should be presented to the Principal Teacher on arrival for inspection. Students should not use machine tools in which they have not been trained or in which they have not reached an acceptable level of competence, and they must not use any machine tools without supervision.
A blank Record of Workshop Experience can be obtained from the Documents Download page.
Preparation for craft skills takes place within the Technology Craft Workshop Courses for one day a week from Years 1 to 3. A map of the core machines, tools and processes that students cover by year is shown below:
Woodworking: Minimum Requirements for Year 2 Placement
(S1/S2 Focus)
Marking Processes:
Use of Face Side & Face Edge, use of marking gauge, tri-square, steel rule.
Cutting/Shaping:
Tenon saw, coping saw, smoothing plane, bevel edged chisel, firmer chisel.
Assembly:
Sash cramps, vice. Gluing/removal of air and so forth. Basic clamping of artefacts with 2-3 parts.
Finishing:
Surface preparation: use of grades of glass paper.
Parafin/BreeWax, low-end Oils such as Linseed and Olive.
Powered Hand Tools:
Hand sander (oscillating)
Pedestal Drill
Use of twist drills, flat bits/forstner bits.
Belt Sander
Perimeter Shaping and Chamfering.
Scroll Saw
Perimeter shaping, splitting timber to recess shapes.
Mortise Machine
Correct setting and use for Mortise Housings.
Pyrography/Wood Burners (if and where possible)
Free hand and against metal templates.
Additional & Miscellaneous:
De-cupping stock timber (split & flip)
Knowledge/Awareness of rip/cross-cut/panel saws.
Metalworking: Minimum Requirements for Year 2 Placement
(S1/S2 Focus)
Marking Processes:
Scriber, Engineer’s Square, Odd-Leg Callipers, Steel Rule, Dividers, Spring Dividers, Centre Punch.
Cutting/Shaping:
Hack saw, Junior Hack Saw, range of files (e.g. 3 edge, square, half round, flat, rat tail: smooth > course). Cross filing/draw filing. Scrolling jig with pre-annealed steel/aluminium.
Assembly:
Snap riveting (set & snap), pop-riveting.
Finishing:
Draw filing, wet & dry paper, fluidiser (dip coating), polishing.
Metal Lathe
Work with round bar and small section square bar (mild steel/aluminium): facing of, parallel turning. Changing cutters, setting height of tool post for given cutters, setting speeds for given cuts. Outside callipers.
Spot Welder
Joining of thin sheet material (e.g 1.6mm mild steel to pre-annealed steel).
Forge
Work with thin bar (e.g. 6mm x 6 mm) Drawing down, tapering, hardening and tempering (including tempering colour matching to application). Use of different tongs, parts of anvil (beak), axial twists with hot work vice, creation of hooks (eyelets also, but not as common). Use of brazing torches for controlled heating of components parts in above processes).
Oven
For evening surface of dip coated components (some school pre-heat larger models prior to dip-coat).
Woodworking: Minimum Requirements for Year 3 Placement
(S3/S4 Focus)
Marking Processes:
Breaking surface fibres, sliding bevels, bradawl, mortise gauge, specific marking of arcs, creation and use of templates and so forth.
Cutting/Shaping:
Surforms, rifflers, rasps, glass paper over files/profiles, dovetail saws, pad saws, flush cut saws, rebate plane, fret saw (deep bow), jack plane, mortise chisel.
Assembly:
More advanced clamping of frames/carcases, methods for squaring and aligning of parts.
Finishing:
Raising the grain, higher-end oils (e.g. hard oil), wax, varnish (% dilutes)
Powered Hand Tools:
Belt sander for material shaping.
Wood Lathe
Turning between centres, use of gouge, scraper and parting tool, staged finishing with multiple grades of glass paper, pre-finish sealing (e.g. melamine lacquer/sanding sealer), finishing with hard wax (e.g. Carnauba) & polishing/buffing.
*can turn segmented material between centres.
Biscuit Jointer
Setting of machine, marking o corresponding material for joining sides lengthwise.
Pedestal Drill
Hole Cutters, Augers, Barrel Sander - perimeter finishing/partial shaping.
Reciprocating Bobbin Sander (desirable)
Perimeter shaping/course finishing.
Additional & Miscellaneous:
Marking and cutting a range of framing joints, including: Mortise & Tenon, Through Mortise & Tenon,
Marking and cutting a range of carcase joints, including:
Parquetry: simple strip/slip patterns.
Electric router for shaping perimeters (*pupils are not allowed to use this machine)
Metalworking: Minimum Requirements for Year 3 Placement
(S3/S4 Focus)
Marking Processes:
Use of marking blue, vee-block, height gauge, Vernier callipers, micrometres (analogue/manual/digital).
Cutting/Shaping:
Tin snips, Cold chisel, bending bars, cutting threads (taps & dies).
Assembly:
Welding/Framing Magnets and clamping. A range of permanent and semi-permanent fixings. Spot welding/tacking.
Finishing:
Range of alternative finishes such as blueing and applied sprays/lacquers.
Metal Lathe
Tapered turning/chamfering, drilling using tail stock (including use of centre bits), knurling, more novel/custom cutters.
MIG Welder
Tacking, folded/seem welds: Joining plates at right angles, joining solid and hollow section to plates, setting up welder feed rate/power for material thicknesses, use of framing magnets and clamping.
Forge
Brazing with spelter rods/flux, surface prep. Heat treatment of materials including hardening, case hardening and tempering.
Box Folder
Sheet metal folding – various.
Woodworking: Minimum Requirements for Year 4 Placement
(S5/S6 Focus)
Marking Processes:
Trammels for marking ellipses, marking geometry for shaped boards (e.g. hexagonal/octagonal), curves/spirals and so forth.
Cutting/Shaping:
Plough plane, hand router, spoke shaves, block plane.
Assembly:
More advanced clamping of frames/carcases, methods for squaring and aligning of parts.
Finishing:
Cabinet scrapers, multi-stage sanding with a range of grades, addressing defects (e.g. wax fills, steaming out gouge marks) prior to application of finish.
Powered Hand Tools:
Belt sander for material shaping.
Wood Lathe
Face plate turning (though not with segmented material)/selbix chuck or similar. Inside calipers, more advanced turning with bespoke/shaped tools.
Additional & Miscellaneous:
Honing plane blades, honing chisels.
Metalworking: Minimum Requirements for Year 4 Placement
(S5/S6 Focus)
Cutting/Shaping:
Fly press (hot/cold work).
Shaping Machine (Optional)
Setting up of machine, channels and surface cuts on a variety of shapes of stock.
Powered Hacksaw
Setting up, clamping material, successive cutting of stock to required lengths.
Bench Grinder
Setting of work plate angle/distance, wheel checks (safety), shaping end of range of bars to a variety of forms.
Milling Machine
Setting up of machine, channels and surface cuts on a variety of shapes of stock.
Metal Lathe
Cutting Threads (desirable).